Herstellung von Membranen und Elektroden
Wir verwenden verschiedene Techniken zur Herstellung von Membranen aus Ionenaustauscher-Polymeren und Elektroden aus Katalysator-Nanopartikeln, -Support und -Binder. Ein entscheidender Faktor für eine effiziente elektrochemische Energieumwandlung ist die Grenzfläche zwischen den einzelnen Schichten, die ausgebildet wird, wenn sie zu einer Membran-Elektrodeneinheit verbunden werden. Hier zeigen wir einen Überblick über die Methoden und Geräte, die in unseren Laboren zur Herstellung eingesetzt werden.
Sprühbeschichtung
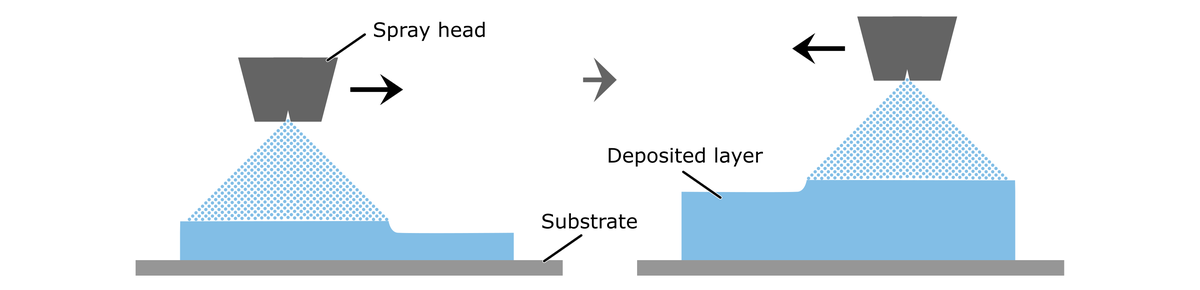
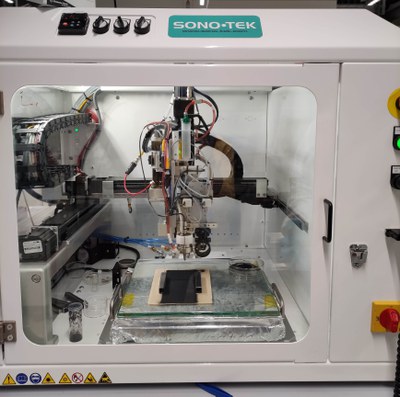
Beim Sprühbeschichten wird eine niedrigviskose Flüssigkeit (zum Beispiel eine Polymerdispersion oder eine Katalysatortinte) über einen Ultraschall-Sprühkopf fein zerstäubt. Die Flüssigkeit wird als feiner Nebel in aufeinanderfolgenden Überfahrten auf einem Substrat abgeschieden. Dort formt sie einen dünnen, durchgehenden Film, nachdem die Lösungsmittel verdampft sind. In diesem Schicht für Schicht ablaufenden Prozess generiert der Sprühbeschichter einen dünnen Film einstellbarer Fläche und Dicke. In unseren Laboren verwenden wir ExactaCoat-Geräte von SonoTek.
Die Vorteile des Sprühbeschichtens liegen in der einfachen Anpassbarkeit der hergestellten Filmdicke, die über die Anzahl an Überfahrten sowie die Flussrate eingestellt werden kann, sowie in der Kontrollierbarkeit der Verdampfungsrate über die Temperatureinstellung des Substrats. Zudem können mittels Sprühbeschichtung nicht nur homogene Lösungen, sondern auch Dispersionen prozessiert werden, also Flüssigkeiten, die einen Anteil an Feststoffen enthalten, wie Katalysator und Binder in einer Elektrodentinte.
Rakeln und Spiralrakeln

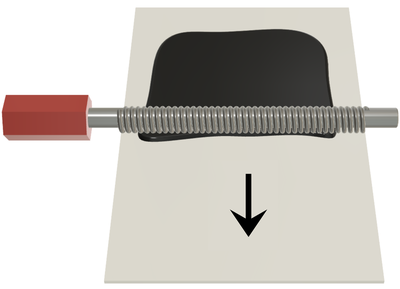
Eine Rakel erlaubt die Herstellung von Membranen und Elektroden aus Polymerdispersionen oder Katalysatortinten. Eine Linie der Flüssigkeit wird auf einem Substrat wie beispielsweise einer Teflonfolie, einer Glasplatte oder einer Gasdiffusionsschicht aufgebracht. Die Rakel wird anschließend mit einem definierten Abstand über dem Substrat sowie mit einer vorgegebenen Geschwindigkeit über das Substrat bewegt, um dieses mit der Flüssigkeit zu beschichten.
Ein Vorteil des Rakelns im Vergleich zur Sprühbeschichtung ist die üblicherweise schnellere Herstellung, da ein Dünnfilm in einem einzigen Schritt hergestellt werden kann. Ein wichtiger Unterschied zwischen Sprühbeschichtung und Rakeln ist die Viskosität der verwendeten Tinten: Beim Rakeln werden hochviskose Flüssigkeiten verarbeitet, wohingegen für die Sprühbeschichtung niedrigviskose Flüssigkeiten benötigt werden.
Die Spiralrakel (engl. Mayer rod) wird zur Herstellung von Elektroden (Katalysatorschichten) genutzt. Das Prinzip der Technik ist ähnlich zum Rakeln, jedoch ist die Oberfläche durch Spiralwindungen strukturiert. Die Geometrie der Spiralwindungen einer Spiralrakel definiert dabei die Dicke des gezogenen Films und unterstützt bei der Erzeugung von gleichmäßigen Beschichtungen.
Elektrospinnen
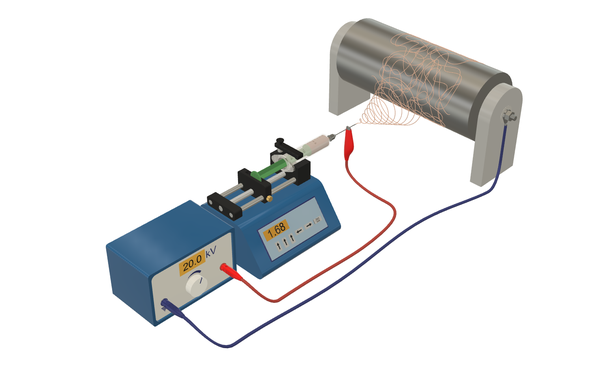
Elektrospinnen wird zur Herstellung von Nanofasern (Polymerfasern mit einem Durchmesser von weniger als 1 µm) eingesetzt. Bei dieser Technik wird eine Polymerlösung über eine Nadel auf ein Substrat abgegeben, auf dem ein Fasernetz gebildet wird. Ein starkes elektrisches Feld zwischen der Nadel und dem Substrat (im Bereich von 10 bis 20 kV) beschleunigt den aus der Nadel dosierten Strahl, der während des Flugs zum Substrat trocknet. Wir verwenden einen Nadel-basierten Lösungs-Elektrospinning-Aufbau der Firma KatoTech.
Die Nanofaser-Netze können aus einzelnen Polymeren, Polymerblends oder Polymerlösungen mit verschiedenen Additiven erzeugt werden. Zur Herstellung von Kompositmembranen können die Fasermatten in die Membranen integriert werden, um beispielsweise als mechanische Verstärkungsschicht zu dienen, oder als chemisch modifizierte Zwischenschicht mit spezifischen funktionellen Gruppen.
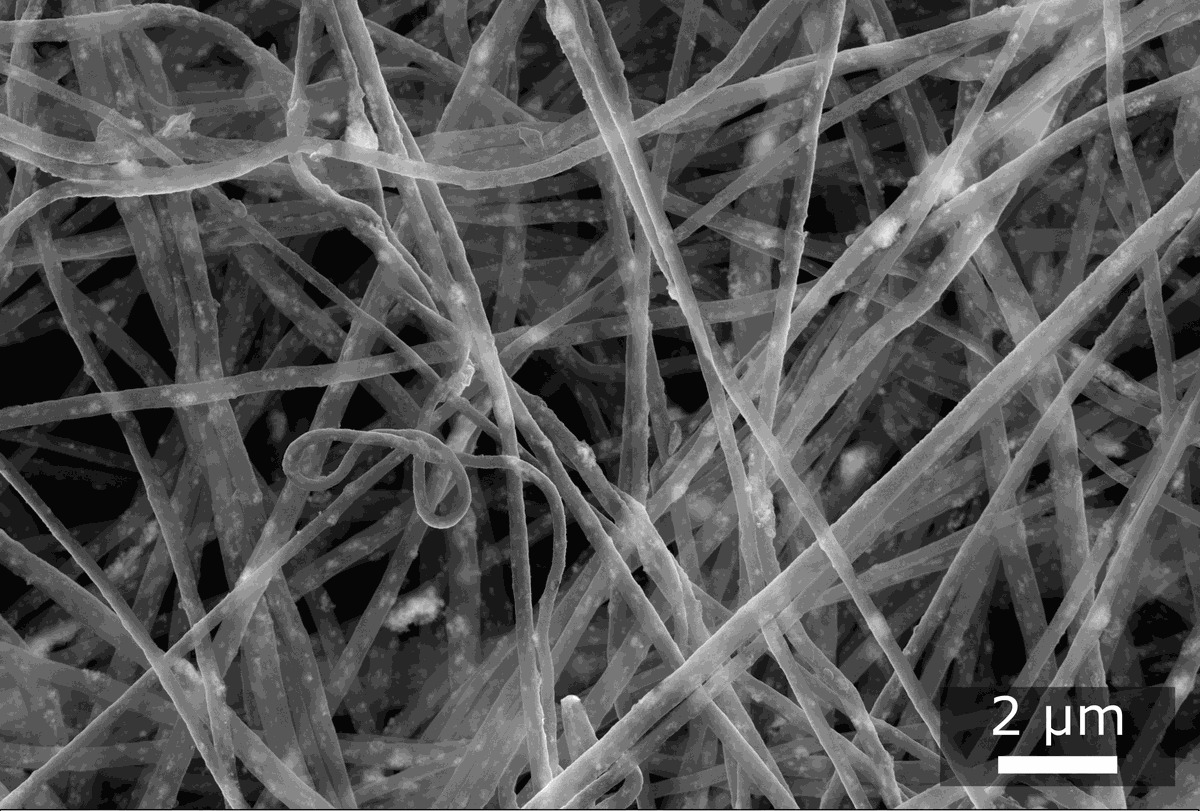
Membran-Elektrodeneinheiten
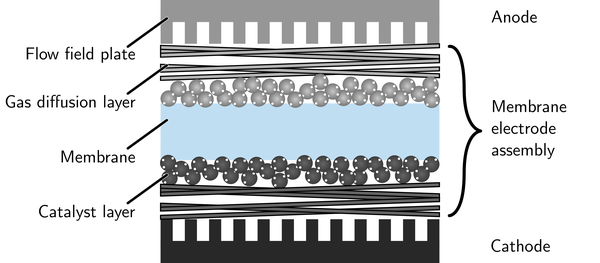
Nach der Herstellung der Katalysatorschichten und Membranen müssen die verschiedenen Schichten miteinander zur Membran-Elektrodeneinheit verbunden werden. Dieser Schritt wird üblicherweise mittels Heißpressen durchgeführt: Die Schichten werden aufeinandergepresst und dabei erhitzt. Als Resultat entsteht eine enge Schnittstelle zwischen den Schichten, die nun eine Katalysator-beschichtete Membran bilden und zusammen mit den Gasdiffusionsschichten als Membran-Elektrodeneinheit bezeichnet werden. Ein guter Grenzflächenkontakt ist unabdingbar dafür, dass die finale elektrochemische Zelle, etwa eine Brennstoffzelle oder ein Wasserelektrolyseur, eine hohe Leistung erreichen kann. Zudem muss die Integrität der einzelnen Schichten gewährleistet sein, um zu verhindern, dass es zu Gasübertritten durch die Membran oder zu elektrischen Kurzschlüssen kommt.
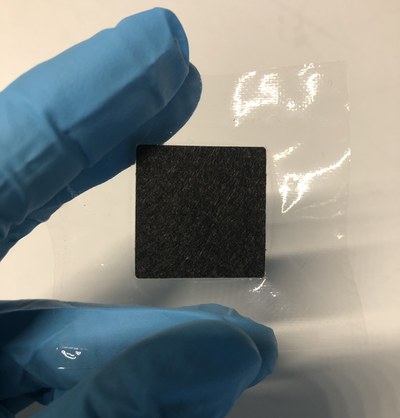
Schließlich wird die elektrochemische Zelle durch den Aufbau der Membran-Elektrodeneinheit zwischen zwei Flussfeldplatten hergestellt. In Wasserelektrolyseuren werden die Diffusionsmedien poröse Transportschichten anstelle von Gasdiffusionsschichten genannt. Letztere ist die Bezeichnung für die Schichten in Brennstoffzellen. Für die Zelle wird außerdem eine Dichtung benötigt, um sicherzustellen, dass sie gasdicht funktioniert. Eine solche einzelne Zelle kann nun betrieben werden, um ihre Leistung, ihre Lebensdauer und ihre Widerstandsfähigkeit gegenüber bestimmten Stressfaktoren zu untersuchen.